Aluminum Casting Mastery: Methods to Elevate Your Manufacturing Refine
Aluminum Casting Mastery: Methods to Elevate Your Manufacturing Refine
Blog Article
Learning Aluminum Spreading: a Deep Study the Different Methods Readily Available
Light weight aluminum casting stands as a foundation of modern-day manufacturing procedures, providing versatility and precision in producing complex layouts and practical parts. As markets progressively turn to light weight aluminum for its light-weight yet durable homes, mastering the numerous spreading methods comes to be critical. From the traditional approach of sand casting to the facility processes of investment spreading and die spreading, each method provides special obstacles and benefits. Recognizing the nuances of these techniques is important for guaranteeing the top quality and effectiveness of the casting procedure. In this expedition of aluminum casting strategies, we will clarify the details of each technique, giving understandings that might reinvent your approach to light weight aluminum casting.
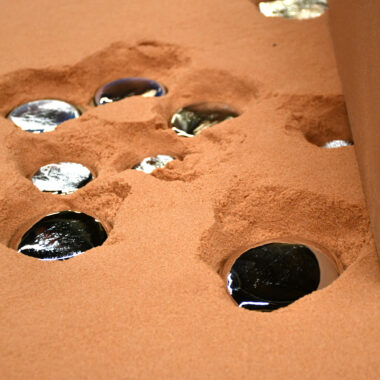
Sand Spreading Strategy Summary
The Sand Casting strategy's flexibility and extensive application make it a cornerstone in mastering aluminum spreading processes. This technique includes producing a mold and mildew from a blend of sand and a binder, such as clay, to form elaborate forms for casting molten aluminum. Sand spreading is a preferred option as a result of its relatively inexpensive, convenience of adjustment, and capacity to produce intricate geometries with high precision.
The process starts with the production of a pattern, usually constructed from wood or steel, which is pushed right into the sand to produce a mold dental caries. When the pattern is eliminated, the mold and mildew cavity is filled up with liquified light weight aluminum, which strengthens to take the form of the pattern. After cooling down and solidification, the sand mold is damaged away, exposing the aluminum casting.
Sand casting is extensively used in various markets, consisting of auto, aerospace, and production, as a result of its adaptability in creating both small and huge light weight aluminum parts (aluminum casting). Its adaptability to complex styles and cost-effectiveness make it a favored selection for numerous light weight aluminum casting applications
Permanent Mold Casting Refine Clarified
Exploring the intricacies of aluminum casting, the Long-term Mold Casting procedure provides a refined method for producing high-grade parts with accuracy and efficiency. Unlike sand casting, long-term mold casting uses a reusable mold generally made of steel or iron to shape the molten aluminum.
Irreversible mold and mildew spreading can be categorized into two main types: gravity spreading and low-pressure spreading. Gravity casting includes pouring the liquified metal into the mold utilizing gravity, while low-pressure spreading utilizes low stress to fill the mold tooth cavity. Both methods use advantages in terms of reducing porosity and boosting mechanical buildings.
Pass Away Casting: Benefits and Disadvantages
Mastering the complexities of die casting includes comprehending its distinct benefits and downsides in the world of light weight aluminum component manufacturing. One essential advantage is the high-speed production ability find out here of die spreading, enabling for the mass production of intricate forms with tight tolerances.
The procedure is not as adaptable when it comes to make adjustments compared to other casting methods like sand casting. In spite of these constraints, the advantages of die spreading frequently exceed the negative aspects, making it a preferred selection for several light weight aluminum casting applications.
Financial Investment Casting Applications and Benefits
Building on the benefits of die spreading, financial investment spreading supplies a versatile approach for producing elaborate light weight aluminum elements with unique benefits in numerous applications. Investment casting, also referred to as lost-wax casting, excels in developing complicated shapes that would be difficult or impossible to accomplish via various other methods. This technique is extensively utilized in industries such as aerospace, automotive, and jewelry making.
One of the crucial advantages of investment spreading is its ability to create near-net form parts, reducing the requirement for extra machining and decreasing material waste. This results in cost savings and faster manufacturing times contrasted to traditional machining procedures. In addition, financial investment casting enables the manufacturing of parts with superb surface finishes and limited tolerances.
In the aerospace sector, investment spreading is preferred for its capacity to create lightweight yet solid elements essential for aircraft performance. The auto sector gain from financial investment casting for creating parts with high dimensional accuracy and elaborate styles. On the whole, financial investment spreading provides a precise and cost-effective option for manufacturing complex light weight aluminum components across different markets.
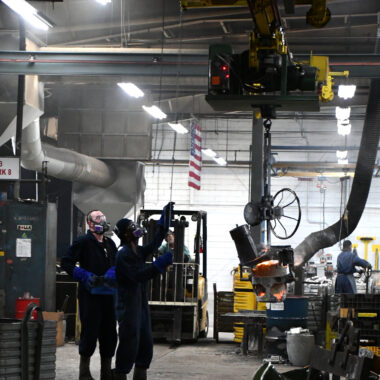
Lost Foam Casting: Just How It Functions
Shed foam casting, also referred to as evaporative-pattern spreading, is an approach for creating intricate metal components by utilizing foam patterns that vaporize throughout the casting informative post process. This technique begins with read here a foam pattern of the desired component being put right into unbonded sand. The foam pattern is commonly covered with a refractory product to boost the surface area coating of the last metal component. When molten steel is poured into the mold, the foam vaporizes because of the warm, leaving a dental caries that is then filled by the steel.
Among the essential benefits of shed foam casting is its capability to produce complicated forms with complex information that might be challenging to accomplish with various other casting techniques. Furthermore, the process can be cost-efficient as it eliminates the requirement for cores and allows for the combination of multiple components into a single part. Nonetheless, it needs careful control of the process parameters to make sure correct foam evaporation and steel flow.
Conclusion
In conclusion, understanding light weight aluminum casting entails understanding and making use of different strategies such as sand casting, permanent mold casting, die spreading, financial investment casting, and lost foam casting. Each technique has its own advantages and applications in the production process. By familiarizing oneself with these various methods, makers can choose one of the most appropriate spreading technique for their specific demands and needs, eventually causing reliable and effective manufacturing of light weight aluminum parts.
From the standard approach of sand casting to the facility processes of investment spreading and pass away casting, each strategy offers unique difficulties and advantages. In this expedition of aluminum spreading methods, we will certainly drop light on the details of each technique, giving insights that could change your strategy to aluminum casting.

Report this page